2025 Copyright – KOCH GmbH | Graphics & concept with ❤ from the Lower Rhine – EHRENPLATZ
Introduction to the world of veneers
Veneers - The art of wood finishing.
Veneers are thin sheets of real wood that are cut or peeled from a tree trunk. They offer the possibility of achieving the appearance of solid wood with less material and at lower cost. This technology not only enables more efficient use of wood resources, but also opens up creative design possibilities.
We always offer you a large selection of more than 100 different types of wood. Other types of wood not listed are available on request.
We stock all standard thicknesses 0.5 / 0.6 mm as well as special thicknesses in 1.0 mm / 1.4 mm / 2.4 mm and 5.00 mm sawn veneers.
Our stock program (excerpt)
Our veneers
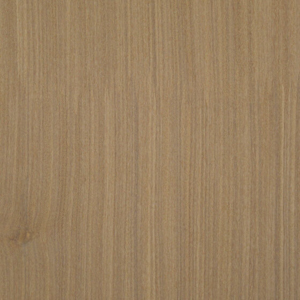
Afromosia
Formats and available thicknesses:
On request!
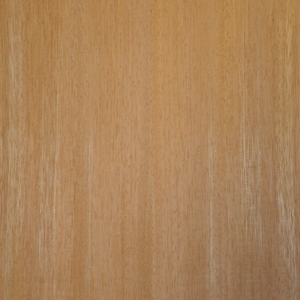
Afzelia / Doussie
Formats and available thicknesses:
On request!
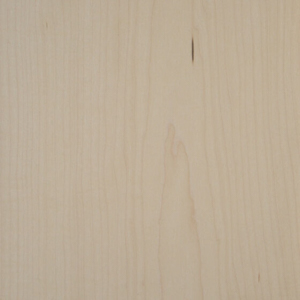
Ahorn amerik.
Formats and available thicknesses:
On request!
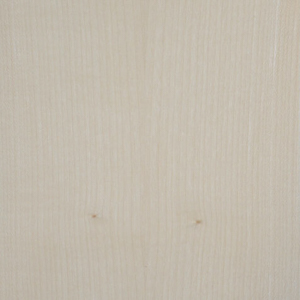
Ahorn europ.
Formats and available thicknesses:
On request!
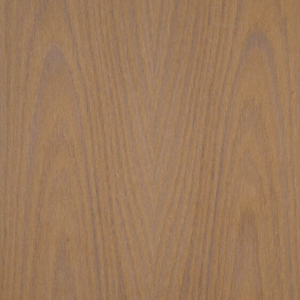
Akazie
Formats and available thicknesses:
On request!
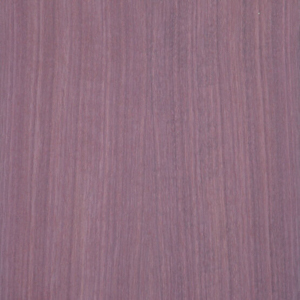
Amarant
Formats and available thicknesses:
On request!
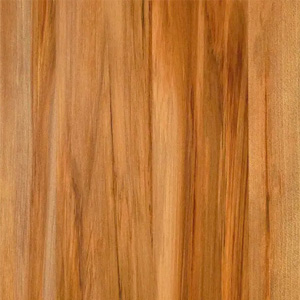
Amber
Formats and available thicknesses:
On request!
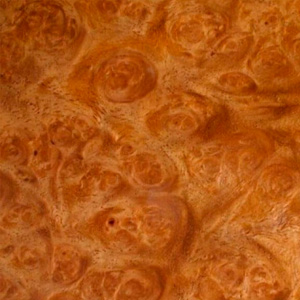
Amboina
Formats and available thicknesses:
On request!
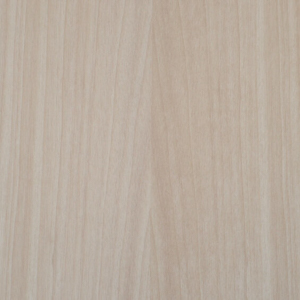
Anegre
Formats and available thicknesses:
On request!
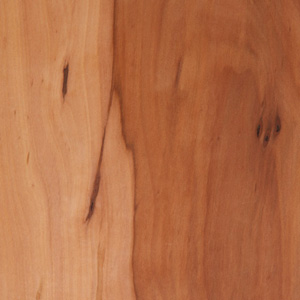
Apfelbaum
Formats and available thicknesses:
On request!
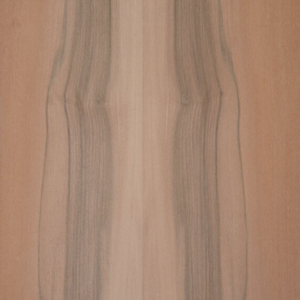
Apfelbaum ind.
Formats and available thicknesses:
On request!
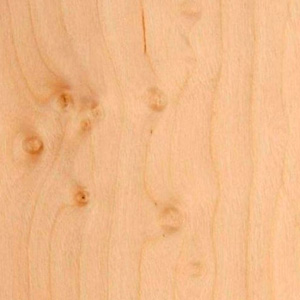
Apfelbirke
Formats and available thicknesses:
On request!
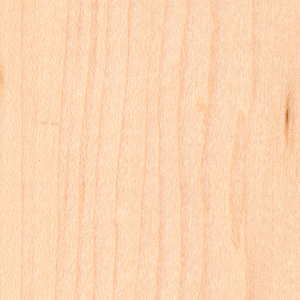
Astahorn
Formats and available thicknesses:
On request!

Asteiche
Formats and available thicknesses:
On request!
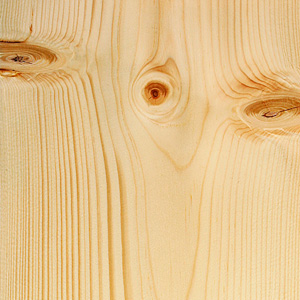
Astfichte
Formats and available thicknesses:
On request!
Introduction to the world of veneers
History, production and types of veneers
Origins of veneer technology
The art of veneering is an ancient craft technique whose origins can be traced back to ancient Egypt. Over 4000 years ago, the Egyptians were already using thin sheets of wood to decorate and reinforce coffins, furniture and other objects. These early veneers were cut by hand, a technique that not only required a high degree of skill, but also increased the value and exclusivity of the end product.
Over the centuries, the technique of veneering spread across the Middle East and later to Europe. Veneering became particularly popular in Italy during the Middle Ages and the Renaissance, where craftsmen began to use veneers not only for their functional properties but also for decorative purposes. They developed complex patterns and inlay work that featured rich geometric and figurative designs and adorned the furniture and interiors of the wealthy and aristocratic classes.
With the industrial revolution and the invention of the steam engine in the 18. and In the 19th century, veneer technology underwent significant further development. Mechanical saws and later veneer peeling machines made it possible to produce veneers faster and in more uniform thicknesses. This lowered costs and made veneered products accessible to a wider audience.
The manufacturing process
The modern veneer manufacturing process has developed into a highly technological and efficient method that emphasizes precision and sustainability. The process begins with the selection of the wood. Only the best and healthiest tree trunks are used for veneer production. This selection is crucial, as the quality of the raw material directly influences the aesthetics and quality of the finished veneer.
After selection, the trunks are prepared, which often involves removing the bark and cutting the trunk into manageable sections. Different methods can be used depending on the desired veneer type and thickness:
-
Sawing: Traditionally and still used for thicker veneers. This method produces little waste but retains the grain of the wood and is ideal for high-quality applications.
-
Peeling: In this process, the tree trunk is rotated around its own axis while a long, thin veneer sheet is continuously peeled off. This method is particularly efficient for the production of veneers from fast-growing, less dense wood species.
-
Knives: Similar to peeling, but the log is not turned. Instead, the knife moves linearly along the log, allowing precise control over the thickness of the veneer. This method is particularly suitable for fine, decorative veneers.
After cutting, peeling or slicing, the veneer sheets are dried. This step is critical to avoid warping and cracking and to ensure the stability of the veneer. Modern drying processes use both air and heat to achieve uniform drying.
The final step in the manufacturing process is cutting and sorting the veneers. They are sorted according to quality, grain and color to ensure that the end product meets expectations. High-quality veneers can also be combined into larger panels to meet specific design requirements.
Different types of wood
The variety of wood species used for veneers is almost limitless and reflects the enormous diversity of our planet's forests. Each type of wood has its own unique properties, colors and grains, which make it possible to create individual and characteristic surfaces.
Exotic and native wood species
Exotic wood species
Exotic woods come from tropical forests around the world and are known for their striking grains and intense colors. Popular exotic veneer woods include mahogany, teak, wenge and zebrano. These types of wood are often the choice for high-quality pieces of furniture or decorative accents that are intended to make a statement.
Native wood species
Native woods, on the other hand, come from the forests of the respective region and offer a palette of rather subtle colors and grains. Oak, beech, maple and cherry are examples of native veneer woods commonly used in Europe and North America. They offer a timeless aesthetic and are extremely versatile.
Specific properties
Each type of wood has specific properties that make it suitable for different applications. The hardness of the wood, its resistance to moisture and the way it reacts to processing are important factors to consider when choosing the right veneer wood.
- Hardness: Hard types of wood such as oak and teak are resistant to wear and tear and are therefore particularly suitable for floors or work surfaces.
- Moisture resistance: Wood species such as teak have natural oils that make them resistant to water and rot, ideal for use in damp environments or outdoors.
- Processing: Soft wood species such as pine are easier to process and are therefore suitable for detailed inlay work or furniture with complex shapes.
Different types of cuts
The way in which a veneer is cut from the tree trunk plays a decisive role in the appearance of the finished veneer. The cut influences the grain and the overall appearance of the wood.
Flap cut
The flap cut is made parallel to the tree axis and produces veneers with a characteristic, often very even grain. This type of cut is particularly popular with oak, as it emphasizes the typical medullary rays of the oak and creates a striking, radial pattern.
Radial cut
In radial cutting, the veneer is cut along a radius from the center of the log. This technique results in a very straight grain with little variation, which creates a very calm and uniform appearance. Radial-cut veneers are particularly valuable for large-area applications where a uniform appearance is desired.
Tangential cut
The tangential cut, also known as the end grain cut, is made parallel to the direction of growth of the tree rings. This cut creates a lively and often dramatic grain that is used for dynamic and eye-catching surfaces. Tangential cut veneers show the natural beauty and variety of the wood grain to its full extent.